What is Total Productive Maintenance?
Total productive maintenance (TPM) is a holistic approach to equipment maintenance that aims to eliminate defects, breakdowns, small stops or slow runs, and consequently, accidents. The main goal of TPM is to improve the quality of systems and integrity of production through the combined use of equipment, supporting processes, and employee expertise.
Benefits of Total Productive Maintenance
One of the most significant benefits of total productive maintenance is its impact on overall equipment effectiveness (OEE). TPM goes against the famous saying, “don’t fix it if it isn’t broken,” because it places preventive maintenance at the forefront and machinery as the core focus of operations.
With the emphasis on prevention and a proactive approach, total productive maintenance can help maximize the operational efficiency of equipment. Another benefit of TPM implementation is being able to encourage the full involvement and participation of workers and equipment operators, while improving productivity.
The 8 Pillars of TPM
The traditional TPM approach is based on the principles of 5S, with an additional eight pillars that are focused on preventive techniques that help improve equipment reliability. The main benefit of introducing 5S as a foundation is to help standardize maintenance processes into everyday activities. This foundation also helps make achieving the 8 pillars below possible.
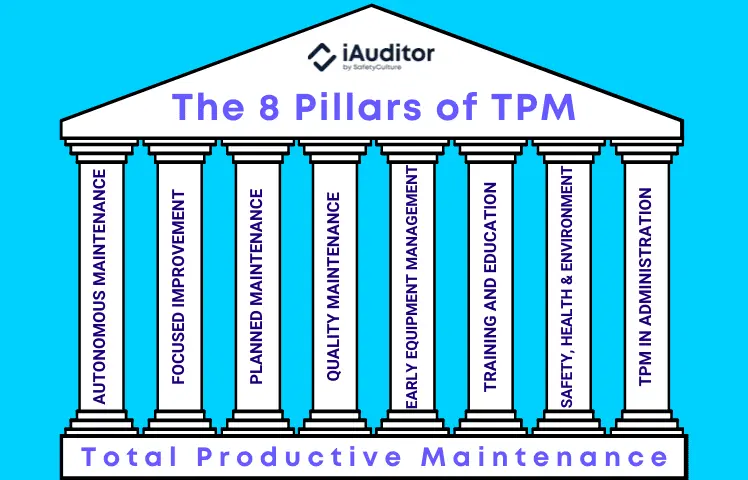
The 8 Pillars of TPM: Total Productive Maintenance
1. Autonomous maintenance
This entails providing machine operators the proper training so they can be solely responsible for routine maintenance operations. This provides a feeling of ownership and accountability while also increasing their knowledge about specific equipment.
2. Focused improvement
This pillar is based on the principles of kaizen, a Japanese term that translates to “good change.” The main goal of kaizen in manufacturing is to ensure that there’s constant improvement in an organization’s processes and functions. Focused improvement places focus on both the processes and the teams that make them happen, encouraging cooperation and collaboration in implementing regular, incremental improvements to processes involved in equipment operation.
3. Planned maintenance
This pillar bases equipment maintenance schedules during the times when it will cause minimal to no disruption in production. It involves analyzing metrics like historical downtime and failure rates and creating a maintenance schedule based on these downtime periods.
4. Quality maintenance
This focuses on providing the best maintenance possible to equipment by conducting a 5 whys analysis to identify the root cause of defects and prevent their recurrence.
5. Early equipment management
This focuses on the creation and design of new equipment. It takes everything learned from the TPM program and uses this knowledge to improve the design of new equipment to ensure reliability and maintainability.
6. Training and education
This ensures that machine operators and other workers are educated and trained on the machines they operate, ensuring that any knowledge gaps that could adversely affect the TPM program are addressed.
7. Safety, health, and environment
Aside from keeping equipment in good shape, an organization must also provide employees a safe, healthy environment to work in. Any process or solution that’s part of the TPM program should have the safety and health of employees as a top priority.
8. TPM in administration
As the name suggests, total productive maintenance should go beyond equipment maintenance and ensure that administrative functions are also efficient. A streamlined administrative process ensures that production is waste-free and will proceed as smoothly as possible.
TPM Programs and OEE
OEE is often used as a reactive indicator metric of a TPM program because it covers the three main factors related to equipment effectiveness, namely, performance, quality, and availability. Creating an effective TPM program starts with the formation of small, multidisciplinary teams that can address core areas, including autonomous maintenance, training of machine operators, and standardization of processes. All teams are encouraged to work together to increase overall productivity and decrease downtime through enhanced reliability of equipment.
While maintenance personnel should be responsible for the TPM program’s major processes, input should be gathered from machine operators or the persons who use the machines on a regular basis. Doing so will help the organization gain visibility of OEE and ensure its continuous improvement. The TPM program should ideally foster an atmosphere of shared responsibility for equipment because this will help reduce cycle times, increase uptime, and eliminate defects, which in turn contribute to improving overall productivity.
The 6 Big Losses
The six big losses are what a TPM program aims to minimize, if not eliminate completely. Equipment-based losses are categorized into the following:
1. Unplanned stops
Unplanned stops refer to sudden or unexpected equipment failures, including electrical failure, mechanical failure, and structural failure, that significantly affect production.
2. Planned stops
This refers to the downtime that occurs in between production processes when equipment needs to undergo setup and adjustment to meet the requirements of producing another part.
3. Small stops
Small stops or idling due to temporary equipment malfunction interrupts production and leads to longer cycle times and increased costs.
4. Slow cycles
If equipment design speed differs from actual operating speed, this leads to loss and extra cost. All parts should be able to run at a machine’s maximum rate.
5. Production defects
This refers to loss of quality caused by malfunctioning equipment. The main factors that contribute to this loss are equipment maintenance and the skill level of the machine operator.
6. Startup defects
This refers to the losses that occur in the early stages of the production process.