What is Value Stream Mapping (VSM)?
Value Stream Mapping (VSM) is one of the key principles of lean manufacturing tools about having an overview of the end-to-end process (from the supplier until the product reaches the consumer) to help analyze and manage the flow of materials and information, identify waste, and determine which step or items do not add value from the customer’s standpoint.
VSM is also known as “material-and-information-flow mapping.” It uses a system of standard symbols as representation of the flow of goods. A study from the American Society for Quality (ASQ) defined it as “the process steps from order entry to delivery.” An excellent simple definition of VSM is from Cutter: “Value stream mapping (VSM) is a Lean manufacturing method used to analyze and manage the flow of materials/information/product to be able to bring a product to a customer. Items are mapped as ‘adding value’ or ‘not adding value’ from the customer’s viewpoint, with the purpose of uncovering whatever doesn’t add value.”
Simply put, VSM is a lean technique for finding and eliminating waste in the process flow that will eventually contribute to efforts for continuous improvement.
6 Key Lean Manufacturing Tools
The origins of VSM are often attributed to Toyota Motor Corporation that popularized lean manufacturing. Being “lean” focuses on eliminating the “mudas” in manufacturing to achieve its main goal of creating more value for customers. Below is the 6 key tools used in lean manufacturing to eliminate waste in the processes:
- Value Stream Mapping (VSM) – a visualization tool used to identify waste in the process and the value added by each step of the process
- 5S Lean – a systematic way of organizing workplaces by eliminating waste using the 5S pillars: Sort (Seiri), Set in Order (Seiton), Shine (Seiso), Standardize (Seiketsu), and Sustain (Shitsuke)
- Total Productive Maintenance (TPM) – is an approach to proactive and preventative maintenance of equipment to avoid breakdowns and defects
- Single-Minute Exchange of Die (SMED) – is a system for reducing the time used for changeovers
- Poka-Yoke – is a work standardization technique used for correcting potential defects
- Kaizen – is a Japanese business philosophy that means, “continuous improvement” or “change for the better”
The philosophy behind all Lean tools is to eliminate waste from your processes in order to maximize the profit. Details such as who is participating in the process, what processes are taking place, and how much time each process is taking are also emphasized.
Goals of VSM
The goal of VSM is to critically address every step in the manufacturing process in order to do the following:
#1 Identify Waste
Waste can come in the form of time, material, and labor. But it may also be related to the utilization of labor as well as poor planning. Below is an infographic from Visual Paradigm showing the 8 waste of lean manufacturing in an acronym from the letters of the word “DOWNTIME” to make it easy to remember:
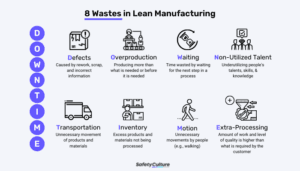
8 Wastes in Lean Manufacturing | Source: Visual Paradigm
Following the identification of wastes, the types of operations or activities that occur during the process flow are determined. There are three types:
- Non-value adding operations (NVA) – pertains to any action that does not add value to a product or service
- Necessary but non-value adding (NNVA) operations – pertains to the activities or processes that are not creating value for the customer, but they are essential to your business.
- Value-adding (VA) operations – pertains to the value given by your customers because value is always determined by the customer; this is what the customers are paying for.
#2 Reduce Process Cycle Times
VSM provides a clear view of the work process—the kind of activities involved. This is also to visualize the process cycle time or how long does one process take for items to go through them. Once the waste has been identified there will automatically be a reduction in process time. This results in a more optimized process.
#3 Eliminate Handoffs
Handoffs means “wait-time” or when one worker needs to wait for another to complete some task. They are most commonly the place or time where things go wrong. Lack of communication can cause delays and waste. VSM identifies handoffs and helps in establishing what’s working and what could be improved.
#4 Implement Continuous Improvement
Using VSM enables you to identify where the sources of waste are and how much time in every cycle is used in every step of the process, giving you opportunities to save time and reduce production cost. Its goal is to make businesses see improvement areas to help them grow and scale successfully.
More Lean Tools for Identifying Value and Waste
There are a number of lean techniques available to help the company identify high-value activities as well as waste.
- 5 whys – pertains to the lean technique of finding the root cause of any problem to identify opportunities for improvement
- A3 problem-solving – pertains to the lean technique of finding the root cause analysis which can often facilitate the identification of value-adding activities and the elimination of inefficient operations
- Gemba walks – pertains to a technique that allows higher management to observe how the work is done and see where value is created
Steps on Creating a Value Stream Map
Value stream maps can be created with flowchart illustration or with softwares like autoCAD by following the steps below given by Visual Paradigm:
Step #1: drawing the process boxes that will be provided with the different process steps, starting from the supplier side going to the customer side in the information flows area.
Step #2: drawing process boxes which will be provided with the different kinds of production steps under the material flows section
Step #3: drawing of data boxes under each box for production steps, in which data is captured of each of the process steps drawn in the map.
Step #4: drawing the connection methods like the push arrows symbols between the process boxes.
Step #5: drawing the link between the suppliers and customers. The last step is the lead time ladder, which can be found at the bottom of the map. It shows the process cycle time in the value stream.
An illustration below shows what a typical value stream map look like:
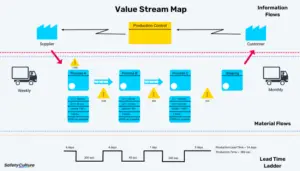
Value Stream Mapping Template | Source: Visual Paradigm
A value stream map helps you see where you can improvise and station your unused or misused resources to produce good work.
- The top section of a VSM is where the information flows. The people involved in the flow e.g., supplier, manufacturer/manager, and consumer are where the activities in the process will come from. For example, the customer gives the details of what they want and when they need it. Then, the manager gives orders and directions on how to do it and where to source it. tell you what they want, where they want and when they want it.
- The middle section is where the material flows. This comprises all processes involved in making the product—from acquiring raw materials from the supplier down to the completion of the product.
- The bottom section is where the lead time ladder is located. It shows all time taken for each and every cycle or process and the gaps between two process steps or the downtime. When the type of activity is determined, whether VA, NVA, or NNVA, it will help eliminate downtime.
See list of typical symbols or icons used in value stream maps here: Project Engineer
Kinds of Value Stream Maps
There are two kinds of value stream maps:
(1) Current state value stream map – this is created before making the future VSM through analysis and tracking of the information and material flow. This is used to determine what the process looks like at the present time; and
(2) Future state value stream map – this focuses on what the future value stream map will look like—including the ideal improvements to the process.
Digitize the way you Work
Empower your team with SafetyCulture to perform checks, train staff, report issues, and automate tasks with our digital platform.
Get Started for FreeSteps to Value Stream Mapping
To properly analyze all the flows and processes involved in the delivery of products or services to the customer, mapping is used.
Here are 7 steps from on how to analyze any manufacturing processes:
- Document the current process – list down all the current activities that are taking place.
- List down all the steps in the process – list down all the stages from the start up to the stage where the demands of the customer is met.
- Identify which steps add value – list down all the steps that adds value to the customer and which do not. Then, determine what can happen if those steps are taken out from the process.
- Visualize what the process will look like when all waste are eliminated – you need to define what it would look like if you could eradicate all waste and activities that do not add value.
- Identify those parts of the current process that hinders the way to achieve your ideal process.
- Determine what areas can be improved and develop possible ways to improve them – this may mean an upgrade to equipment or tools. This could also mean that you need to add more people or your workers need additional training.
- Assign tasks and implement the plans – this step is the stage where assignments are designated to the appropriate persons or groups to properly execute the plans.
SafetyCulture (formerly iAuditor)for Value Stream Mapping
VSM was originally created using paper that could get messy, hard to manage, and hard to understand as the processes and data keep piling up. Using a software to digitize your processes is an easier and more effective way to map your business flows. It will also be more efficient to share it throughout the entire organization if you have a platform for it.
Get a better solution with the help of SafetyCulture, the best digital tool you can use to accurately build up the information you need for analysis and identification of waste in your processes. You can also use SafetyCulture to:
- Annotate in documents or make changes to information in the data boxes that will be changed for the whole organization to see in real time.
- Share the information more conveniently with the cloud feature that can be accessed anywhere in a mobile app.
- Monitor your team’s performance with the real-time monitoring and KPI monitoring feature.
- Conduct equipment management with digitized inspections to ensure that they will run smoothly during the operations to prevent defects and downtime.
- Check the quality of your production and end-products with quality control check sheet to ensure that it meets the expectations of the customers.