What is Directional Boring?
Directional boring, also known as Horizontal Directional Drilling or HDD, is a method of installing various types of underground utilities, such as pipelines and cables, without disturbing the surface above. It is often used in areas where excavating or trenching is not practical or possible, such as beneath roads, buildings, or other sensitive structures.
The process of directional boring begins with drilling a small pilot hole. This pilot hole is then enlarged to a size that is sufficient for the installation of the desired underground utility. Once the pilot hole has been enlarged, the direction of the bore is changed in order to reach the desired location.
Directional boring is a relatively new technology, but it has been growing in popularity in recent years due to its many advantages.
What are its Pros and Cons?
Directional boring is often used to install water and gas lines, sewer and storm drains, and even power and communications cables. There are many advantages to using the HDD method, but there are also some disadvantages to keep in mind.
Advantages
Directional boring has a number of advantages over traditional excavation and trenching methods. It is less disruptive to the surface, so it can be used in areas where traditional digging would not be possible, such as busy streets or fragile ecosystems. It is also less expensive and time-consuming than trenching and can be used to install multiple lines at once.
Streamline Your Construction Operations
Unlock the power of data-driven insights, standardized processes, and effective communication to improve efficiency and productivity across all jobsites.
Explore Our Construction Operations SolutionDisadvantages
Directional boring also has some disadvantages. It is a more complex process than trenching, so it requires more training and experience to do it correctly. It also has a higher risk of damaging the underground infrastructure, which can be extensive and expensive to repair.
How Does Directional Boring Work?
There are several processes that need to be done when performing HDD operations. Some of these include:
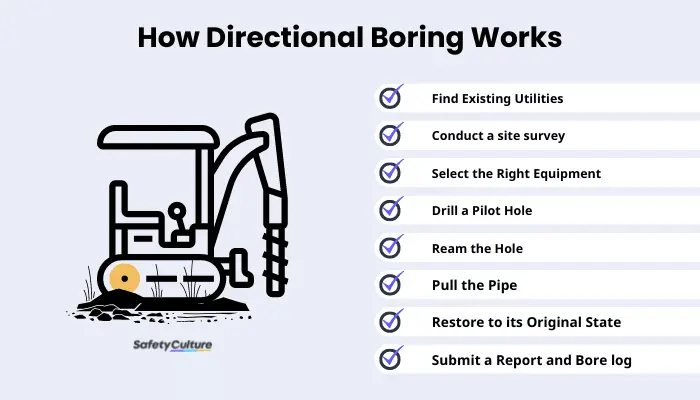
Directional Boring Process: How It Works
1. Find Existing Utilities
You need to know where all of the existing utilities are before you start to bore. This way, you can avoid them and not cause any damage.
2. Conduct a Site Survey
Once the utilities are located, the next step is to survey the site. Usually conducted by a boring foreman or project manager, a site survey helps determine the best route for the bore, taking into account such factors as terrain and underground obstructions.
3. Select the Right Equipment
After the survey is complete, the next step is select the equipment that will be used for the bore. This includes choosing the right drill, deciding on drilling fluid, and selecting reaming equipment.
4. Drill a Pilot Hole
After choosing the appropriate boring equipment, the pilot hole is drilled first using a smaller diameter drill bit. This helps establish a starting point and makes it easier to pull the larger drill through afterward.
5. Ream the Hole
Once the pilot hole is drilled, the reamer is pulled through to widen it out to the final size. This is usually done in several passes, gradually increasing the size of the reamer each time.
6. Pull the Pipe
Next, the pipe is pulled through the newly created hole. This pipe is usually made of High-Density Polyethylene (HDPE) and can be used for various purposes, such as carrying water, gas, or telecommunications cables.
7. Restore the Site to Its Original State
Once everything has been carried out, it’s time to do site cleanup and restoration. This process involves the removal of extraneous bore mud and spoils using a vacuum excavator. Meanwhile, surface features such as sod, asphalt, and curbing are restored to their initial condition.
8. Submit a Report and Bore Log
Finally, field personnel must submit a report which includes the details of the utilities installed and a bore log that indicates the depth and path information to the customer. A digital log template can simplify this documentation process for field operators.
Applications of Directional Drilling
Here are some of the most common applications for directional boring:
- Installing drainage and sewer pipe systems
- Drilling to avoid geological problems
- Placing utility lines beneath sidewalks and streets
- Installing cable television and telecommunications lines
- Drilling for environmental remediation purposes
- Drilling for oil and gas exploration
- Constructing Tunnel Boring Machines (TBMs)
FAQs about Directional Boring
Yes, directional drilling is also known as directional boring in construction sites. Other names for directional boring include Horizontal Directional Drilling (HDD).
The common tools and equipment used in directional boring are drills, drill pipes, reamers, casing pipes, mud pumps, and mud pits.
Depending on your area, directional boring usually costs about $6-$8 per foot. Prices may vary depending on the complexity of the boring project, the area to be drilled, and other factors.
Directional boring can reach about 10,000–15,000 feet (3,000–4,500 meters). It can also dig up to about 25,000 feet (7,500 meters) when used under favorable circumstances.