What is DFMEA?
Design Failure Mode and Effects Analysis (DFMEA) is a process done by design engineers to ensure that products perform their intended functions and satisfy user needs. DFMEA evaluates the overall design of product systems and components to determine potential failure modes and causes. Also known as Design FMEA, it specifies recommended actions to eliminate or minimize possible design failure effects on customers. Design Failure Mode and Effects Analysis is especially useful in the manufacturing industry, where risk reduction and failure prevention are critical. Performing an effective DFMEA enables teams to understand their design better, improve its safety, and develop high-quality products.
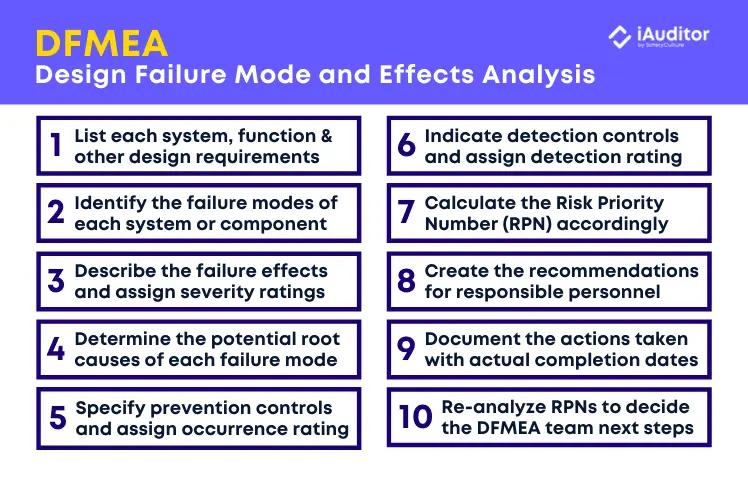
Design Failure Mode and Effects Analysis (DFMEA) Process | How to Perform in 10 Steps
What is the Difference Between DFMEA and FMEA?
The main difference between DFMEA and FMEA is that DFMEA specifically focuses on identifying failure modes, causes, and effects of a product design, while FMEA provides general guidelines which can be applied to a process, service, and more. Design Failure Mode and Effects Analysis is also often related to Process Failure Mode and Effects Analysis (PFMEA), but they differ in which phase of the product development process each of them is conducted.
Why is DFMEA Important?
DFMEA is important because it helps engineers detect and correct potential design failures at the onset, reducing product development time and costs. Following DFMEA process can also result in the creation of a more robust design, having clearly defined requirements. For example, if any component doesn’t have a function, then it shouldn’t be a part of the design.
Who Should be Involved in DFMEA?
A typical DFMEA team includes 4-6 members who understand the design, its requirements, and manufacturability considerations. A product design engineer usually leads this cross-functional team where material, testing analysis, and product quality engineers participate in the DFMEA. Representatives from other departments such as production, service, and logistics can also get involved throughout the procedure.
When Should DFMEA be Completed?
The first Design Failure Mode and Effects Analysis should be completed before the release of drawings to manufacturing and process engineering. This allows adequate time to assess the design prior to analyzing the process for producing the product. Another instance when DFMEA should be done is if the current design will be modified—either as a result of past failure or for further product improvement.
How to Perform DFMEA Process in 10 Steps
Generally, the steps for DFMEA implementation depend on certain company protocols and vary across different sectors such as aerospace, nautical, and automotive. While the process seems intimidating at first, it actually makes sense as a structured and logical approach to analysis. To help teams get started, review this example of how to perform a 10-step DFMEA process:
Step #1: List each system with its function and other design requirements
One of the simplest ways to accomplish this is by breaking down the product design into systems and components, each with its own function, and organizing them in a design and function tree. These visualizations help demonstrate the relationship of the overall design, systems, and components functions. For example, the seat system of a basic chair design might consist of the seat itself (to support the weight of the user), aprons (to reinforce edges of the seat), corner blocks (to attach aprons to the legs), and fasteners (to hold the corner blocks to aprons).
Step #2: Identify the failure modes of each system
A failure mode is a state where a design fails to meet user needs and/or its intended functions, among other requirements. Since a function of the seat system is to support the user’s weight, then a failure mode—one of the ways this system could fail—is that the seat might break.
Step #3: Describe the potential effects of each failure mode and assign severity rating
A failure effect is the direct result of a failure mode that happens. Potential effects of a seat that breaks include the exposure of sharp edges, the collapse of the chair, and the injury of users. Based on a set criteria, a severity rating should be assigned to these failure effects on customers. For example, rating the severity of an effect with 1 means that it contains minimal customer impact, while an effect with a severity rating of 10 means that the design failure affects customer safety or regulatory compliance.
Step #4: Determine the potential causes of each failure mode
After designating a severity rating for a failure effect, look into the root cause(s) of the failure mode. In some cases, a design failure cause lies in component function failures such as thin seats, weak aprons, sheared corner blocks, and loose fasteners for the failure mode “seat breaks”.
Step #5: Specify prevention controls and assign occurrence rating
DFMEA prevention controls are specific measures being done to prevent failure causes from existing. Keep in mind that these refer to current preventive, or preventative, activities. An occurrence rating should be assigned according to how likely a failure cause will remain even with preventive measures already in place. Occurrence ratings can also range from one to ten where 1 means very unlikely or nearly impossible for the cause to occur with ongoing prevention controls, while 10 means very likely or almost a certainty for the cause to still exist, leading to imminent failure.
Step #6: Indicate detection controls and assign detection rating
DFMEA detection controls are existing procedures implemented to improve the capability of recognizing failure causes before finalizing the design drawings and specifications. Current detection activities might involve visual inspections, durability tests, and customer reviews. Whatever the methods, a detection rating should be assigned based on how likely these measures will discover failure causes. Scoring a detective control with 1 means that it can most certainly detect a failure cause, while a detection rating of 10 means that a failure cause may stay undetected even with ongoing controls in place.
Step #7: Calculate the Risk Priority Number (RPN)
In DFMEA, a risk priority number is primarily used to help teams prioritize which design failure modes to address. Get the RPN by multiplying all the DFMEA ratings—severity, occurrence, and detection. It is essential to note that the DFMEA scoring works relative to the other numbers. Suppose 3 different failure modes have RPNs of 60, 120, and 30 respectively, then consider to prioritize dealing with the second failure mode with RPN 120. A pre-determined RPN threshold value (e.g. 100 and above) can streamline the decision-making process for which failure modes to take action as well.
Step #8: Create high-priority recommendations
Upon identifying failure modes with RPNs that exceed the limit, recommended actions with target completion dates should be assigned to responsible personnel. When defining what actions should be taken, think of ways to decrease the severity of failure effects or if new preventive and detective measures can reduce the occurrence and detection scores.
Step #9: Document actions taken
While Design Failure Mode and Effects Analysis can systematically provide sound recommendations, things may not go as planned. Whatever actions taken, they should be documented with the actual completion date. The DFMEA form should also be updated accordingly to help teams follow through and monitor their progress better.
Step #10: Re-analyze RPNs to decide next steps
Finally, the risk priority numbers of target failure modes should be re-computed because actions have been taken to improve the design. When the team acknowledges that changes made have addressed all the risks, then the design can move forward in the product development process.
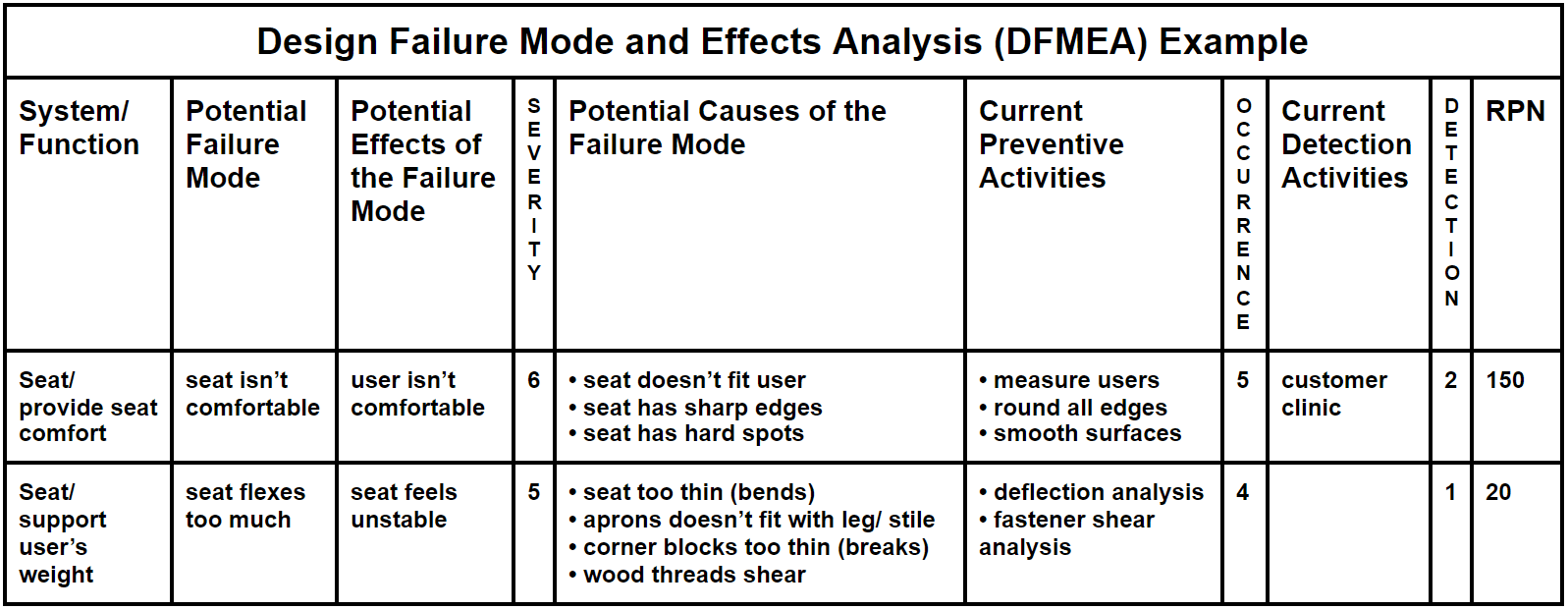
Sample DFMEA Format | Source
Scale Your Enterprise Operations with Customizable Solutions
✓ Scale ✓ Data ✓ Security ✓ Integration ✓ Teams
Learn MoreDFMEA Example: Common Mistakes and Action Plans
Going through the DFMEA process is a rigorous discipline that requires patience and practice. There may be times when it feels like your team is taking two steps forward and one step back. At some point, worry starts to set in as the Design FMEA uncovers the complexity of the product being analyzed. We have rounded up 3 of the most common mistakes DFMEA teams make and what you can do to avoid them:
- Overlooking non-function design requirements: While design failure modes often associate with system functions, other requirements should also be taken into account. For example, there are at least 14 types of design requirements for general products such as cost targets, aesthetics, capacity, inputs/outputs, and environmental, regulatory, or licensing considerations.
- Adding non-root causes as failure causes: It might be helpful to enumerate all possible causes of failure modes, but teams can get the most out of DFMEAs by focusing on tackling root causes alone. Adequate prevention controls can be determined only when root causes are stipulated. Apply supplemental root-cause analysis techniques to ensure teams reach and resolve the failure root cause.
- Generalizing current and planned prevention controls: A detection control is usually much easier to define and set up because of its reactive nature—actions done to spot defects. On the other hand, a preventive control needs to be more specific because as a proactive approach to failure prevention, it has to operate at worst-case conditions. For example, below are some DFMEA prevention and detection controls:
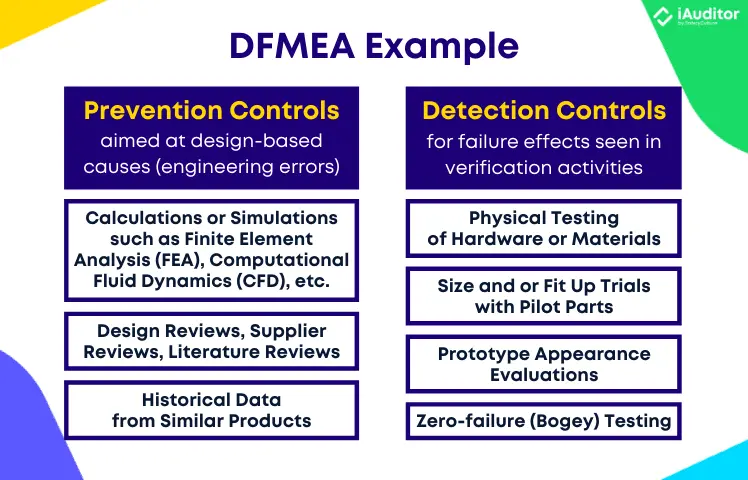
DFMEA Example: Prevention Controls and Detection Controls
Create Your Own DFMEA Template
Eliminate manual tasks and streamline your operations.
Get started for FREE