What is Cleaning Safety?
Cleaning safety refers to the practice of ensuring that people assigned to cleaning spaces and equipment follow the minimum health and safety cleaning procedures, are well-protected during their cleaning tasks, and are kept safe from risks and hazards involved in their job. In the workplace, employees tasked with cleaning must be provided the required equipment, training, and resources by the employer to enforce cleaning safety standards.
Importance
A clean workplace presents many benefits. It can boost productivity, improve safety, prevent health risks, and uplift the overall mood of employees and visitors that come into the workplace. This is why cleaning professionals and workers play a key role in keeping it neat and presentable at all times. Hence, their safety while doing their job must be given importance and attention by their employers.
While cleaning tasks are present in almost every workplace in every industry, it’s quite more obvious and highly important in certain sectors, including:
- Hospitality
- Healthcare
- Construction
- Manufacturing
- Home Services
Workers in charge of cleaning tasks face various risks and hazards depending on the nature of their work and the industry they’re in. These may include musculoskeletal disorders, from manual handling of cleaning equipment to skin complications such as skin allergies, asthma, and burns caused by toxic chemicals found in cleaning agents. This is why enforcing safety measures and guidelines in all cleaning work is important to help ensure workers are protected and safe from dangerous events on the job.
What are the Principles of Cleaning?
To solidify the importance of safety in cleaning, it’s key to learn about the principles or factors that affect cleaning activities. Here are 4 of them that you must know:
- Time – The amount of time spent accomplishing a cleaning task heavily impacts its overall results and quality.
- Temperature – As temperature increases, the process of cleaning becomes easier, faster, and more efficient. However, electricity costs can also become higher, and the risks they pose can become even more serious.
- Chemical Reaction – Identifying the most appropriate chemicals or cleaning agents to use is a must, depending on the level of cleaning needed.
- Procedures – Correct procedures must be performed for the type of cleaning work to be done. Improper implementation can affect the other principles and render them useless in making the process more effective.
What are the Common Cleaning Safety Hazards?
To help promote a culture of safety in an organization, identifying, mitigating, and addressing workplace hazards are a must. In the context of cleaning safety, a variety of risks and hazards can be present and pose threat to the health and safety of cleaning workers. These include the following:
- Slips, trips, and falls
- Confined spaces
- Ergonomics
- Asbestos
- Cleaning chemicals (chemical hazards)
- Molds
- Bloodborne pathogens
Improve your EHS Management
Cultivate a safe working environment and streamline compliance with our EHS solutions.
Explore nowTips
Knowing and implementing the dos and don’ts in cleaning safety can help ensure that your workers are well-guided and protected from the risks involved in their job. Heed these major cleaning safety tips that your organization and workers must follow:
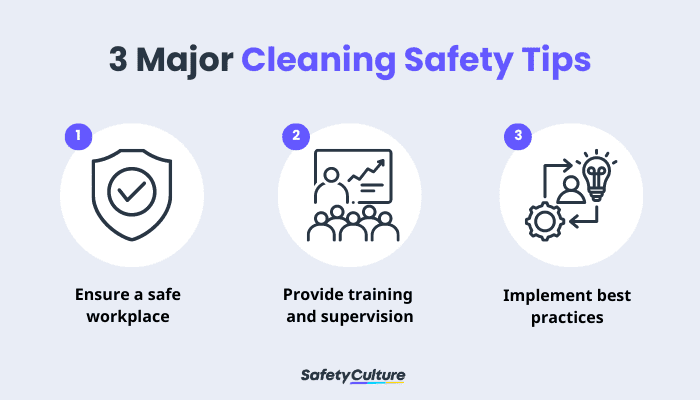
3 Major Cleaning Safety Tips
Ensure a safe workplace.
Make sure that the workplace has enough ventilation or airflow when using cleaning agents that have chemicals. Workers must be able to access and use sufficient Personal Protective Equipment (PPE) such as gloves, safety goggles, and the like as required.
Also, maintain a functioning inventory of supplies and equipment that helps you protect your workers while they’re doing their cleaning tasks. Some of the most important ones you must include are:
Provide training and supervision.
Before any cleaning work commences, sufficient training and guidance must be given. Depending on the type of cleaning activity and equipment or products to be used, the level, frequency, and coverage of training can vary.
As an example, the US Occupational Safety and Health Administration (OSHA) Hazard Communication standard states that the required training employers must provide include the following when dealing with cleaning chemicals:
- Risks and hazards involved
- How to handle, use, and store cleaning chemicals
- What to do in case of spills and other related emergencies
- How to read, process, and refer to labels and Safety Data Sheets (SDS) of cleaning products
Implement best practices.
In this tip, it’s crucial to identify and standardize protocols for handling and accomplishing cleaning activities so that all workers are aligned with best practices and the quality of their work can be improved and maintained. Hence, minimum health and safety standards must be strictly met regularly, with industry-specific guidelines kept in check as part of the organization’s non-negotiables in its overall operations.
Digitize the way you Work
Empower your team with SafetyCulture to perform checks, train staff, report issues, and automate tasks with our digital platform.
Get Started for FreeWhat Regulatory Bodies Govern Safety in Cleaning Practices?
While every state, region, and country may have its own specific laws and policies governing cleaning safety, there are internationally-recognized agencies that serve as regulatory bodies guiding employers globally. Some of these include the following:
Training
As an important cleaning safety tip, a significant amount of attention must be given to training programs that organizations implement. Such initiatives include the use of PPE, cleaning products, and first-aid kits as well as how to address risks and hazards before, during, and after the work.
To help you effectively implement training programs, consider using engaging tools like Training toward promoting a sustainable culture of continuous learning and employee training. It’s a microlearning solution that lets you download editable courses or create from scratch and deploy them to your workers and disseminate best practices across the organization.
To get started, check out these free, editable microlearning courses you can download:
FAQs About Cleaning Safety
It’s key to note that proper timing can do wonders for the success of your cleaning work. Carefully plan out your cleaning approach to help in minimizing exposure to toxic chemicals and be strategic in managing various cleaning tasks simultaneously.
Using cleaning agents can pose serious risks to workers due to their chemical content, ingredients that may affect humans’ breathing, and the possibility to cause skin burns when mishandled. Hence, safety measures such as wearing protective clothing and equipment are advised to help lessen or prevent accidents, injuries, and diseases.
It’s important to ensure that the programs and initiatives you implement in your company fit the needs of the stakeholders. To guide you, the following components must be incorporated into your organization’s cleaning safety training programs:
- Standard Operating Procedures (SOPs)
- Checklists
- Employee handbook
- Training schedules
- Learning resources
- Regular employee evaluations
Workers assigned with cleaning duties must possess key skills to help them ensure their safety while doing their assigned jobs. Some of such skills include the following:
- Knowledge of health and safety protocols
- Understanding of and practical knowledge of using cleaning chemicals, equipment, and other tools
- Time management
- Great attention to detail
- Teamwork
- Excellent organizational skills