Was ist korrektive Instandhaltung? (Definition / reaktive Wartung)
Die korrektive Instandhaltung (auch als ereignisorientierte oder zustandsorientierte Instandhaltung bezeichnet) ist eine Art von Wartung, die von Technikern durchgeführt wird, um eine Fehlfunktion von Geräten, Maschinen und Systemen zu beheben. Sie zielt darauf ab, den guten Betriebszustand und das festgelegte Leistungsniveau der betroffenen Anlagen wiederherzustellen. Die korrektive Instandhaltung wird deshalb auch als reaktive Wartung bezeichnet, da sie erst ausgelöst wird, wenn ein Maschinenausfall bereits eingetreten ist. Sprich, etwas wird erst dann repariert / gewartet, wenn es bereits kaputt gegangen ist.
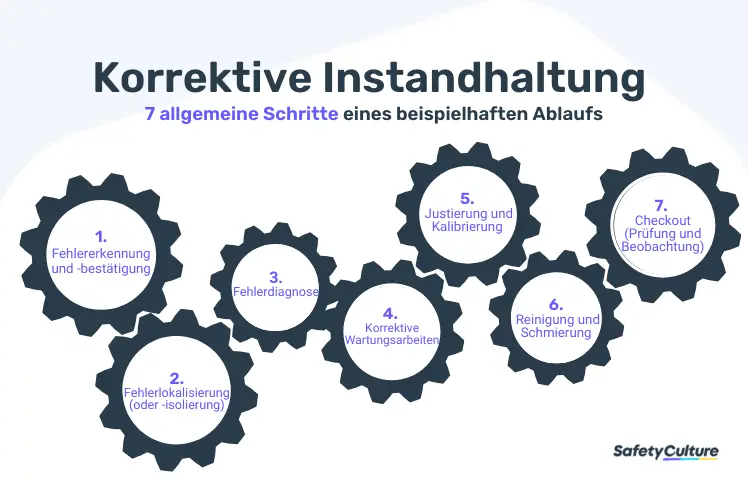
Übersicht über das Verfahren zur reaktiven Wartung | SafetyCulture
Unterschied: Korrektive (reaktive) und vorbeugende (präventive) Wartung
Der Unterschied zwischen der korrektiven (kurativen) und der präventiven Instandhaltung besteht im Allgemeinen in dem Zeitpunkt, zu welchem diese durchgeführt werden.
- Die korrektive Wartung wird nach einem Ausfall der Ausrüstung durchgeführt, um deren Betriebsbereitschaft wieder herzustellen.
- Während die präventive Wartung in regelmäßigen Abständen durchgeführt wird, um das Risiko ungeplanter Ausfallzeiten zu mindern.
Um den Unterschied zwischen korrektiver und präventiver Instandhaltung noch weiter zu verdeutlichen haben wir die folgende Tabelle für Sie zusammengestellt:
Korrektive Wartung |
Vorbeugende Wartung |
|
Hauptzweck |
Zur Wiederherstellung der Funktionsfähigkeit. |
Für den fortgesetzten Betrieb des Systems. |
Art der Aufgabe |
Ungeplant und außertourlich. |
Geplant und terminiert. |
Frequenz |
Jedes Mal, wenn ein Gerät ausfällt. |
Regelmäßig zu einer bestimmten Zeit durchgeführt. |
Allgemeines Protokoll |
Durchführung von Reparaturen: Zum Austausch von Teilen, neuerlichem Zusammensetzen, Einstellen und Prüfen. |
Durchführung von Inspektionen: Erkennung und Vorbeugung drohender Ausfälle. |
Verschiedene Arten der korrektiven Instandhaltung (mit Beispielen)
Bei der korrektiven Wartung wird in der Regel zwischen zwei Arten unterschieden: Instandhaltung bei Ausfall und aufgeschobene Instandhaltung. Nachstehend finden Sie die Definitionen der einzelnen Arten der reaktiven Instandhaltung zusammen mit Beispielen aus der Praxis:
Ausfallwartung
Die Ausfallwartung, die auch als Notfallwartung bezeichnet wird, wird bei einem Maschinenfehler umgehend durchgeführt, um kritische Geschäftsprozesse wiederherzustellen. Ein Stromversorgungsunternehmen repariert oder ersetzt beispielsweise sofort einen durchgebrannten Transformator in seinem Verteilungssystem.
Aufgeschobene Wartung
Die Aufgeschobene Instandhaltung bezeichnet aufgrund unzureichender Ressourcen wie Finanzen, Material und/oder Arbeitskräfte aufgeschobene Wartungsvorgänge. Zum Beispiel könnte die Gebäudeverwaltung die Reparatur von HVAC- oder Klimaanlagen aufgrund fehlender Mittel verzögern.
4 weitere mögliche Aktionen der reaktiven Wartung
Nach Angaben aus dem Handbuch der technischen Planung der US Army (Maintenance Engineering Techniques), gibt es neben der Reparatur oder dem Austausch einer Komponente noch weitere Maßnahmen, die durchgeführt werden können. Im Folgenden werden diese 4 zusätzlichen Aktionen der korrektiven Instandhaltung auf der Grundlage des Handbuchs beschrieben:
- Überholung: Wiederherstellung eines zufriedenstellenden Zustands auf der Grundlage des Wartungsstandards “Inspektion und Reparatur nur nach Bedarf”.
- Wiederaufbau: Vollständige Demontage. Inspektion aller Teile und Reparatur oder Austausch von abgenutzten. Neuerlicher Zusammenbau und Prüfung, um die Anlage in Bezug auf Aussehen, Leistung und Lebensdauer so weit wie möglich in den ursprünglichen (neuwertigen) Zustand zu versetzen.
- Rettung: Teile entsorgen, die nicht mehr verwendbar sind und mit geretteten Teilen aus bereits stillgelegten Anlagen ersetzen.
- Service: Das gezielte Reparieren oder Überholen von Bauteilen oder Komponenten nach der Durchführung einer Fehlerbehebung an einer Maschine.
Wie führe ich die korrektive Instandhaltung richtig durch? (Schritt-für-Schritt-Anleitung)
Die Verfahren der korrektiven Wartung variieren je nach Anlage, vorhandenen Ressourcen und Unternehmensanforderungen. Beispielsweise können Maschinen mit moderner Technologie die Zeit für die Diagnose eines Problems verkürzen und die Reparaturkosten senken, ohne dass die Betriebszeiten negativ beeinträchtigt werden.
Nachfolgend finden Sie einen allgemeinen Ablauf der 7 Schritte zur reaktiven Instandhaltung, um Ihnen den Einstieg zu erleichtern:
Schritt 1: Erkennen von einer Fehlfunktion des Systems.
Ein festgestellter Maschinenfehler muss zuerst von Technikern vor Ort bestätigt werden. Wenn sich herausstellt, dass kein schwerwiegender Fehler vorliegt, wird das System in der Regel einfach wieder in Betrieb genommen. Bestätigt sich jedoch, dass eine Störung vorliegt, müssen korrektive Wartungsmaßnahmen ergriffen werden. Normalerweise muss vor der Durchführung von Instandsetzungsmaßnahmen auch ein Fehlerbericht erstellt werden.
Schritt 2: Eingrenzung des Defekts auf ein bestimmtes Gerät innerhalb der Anlage.
Die Fehlerlokalisierung, manchmal auch als Fehlerisolierung bezeichnet, ist der Prozess, bei dem der genaue Ort des Defekts soweit bestimmt wird, wie es für die Reparatur erforderlich ist. Im Rahmen der korrektiven Instandhaltung wird der Fehler auf ein bestimmtes Gerät innerhalb des Gesamtsystems zurückgeführt. Die Techniker müssen feststellen, in welchem Bauteil der Anlage die Störung tatsächlich aufgetreten ist.
Schritt 3: Diagnose des Schadens an einer bestimmten Komponente des Geräts.
Nach der genauen Feststellung des Fehlers erfolgt die Diagnose des defekten Teils des Geräts. In der Regel wird spezialisierte Hardware oder Software verwendet, um die Ursache der Störung zu ermitteln. Bei den meisten Maschinen kann auch eine eingebaute Testfunktion der vorhandenen Hardware- und/oder Softwarekomponenten dabei helfen ein fehlerhaftes Teil zu identifizieren.
Schritt 4: Reparieren oder ersetzen Sie das defekte Bauteil.
Bei der reaktiven Instandhaltung führen die Techniker Korrekturen durch, wie z. B. die Reparatur oder den Austausch von Maschinenteilen. Dieser Schritt kann auch als “Fehlerbehebung” bezeichnet werden, da bei ihm Wartungsarbeiten zur Behebung der Störung durchgeführt werden. Mit diesem Schritt werden häufig auch grundlegende Messgrößen für die Instandhaltbarkeit wie die mittlere Reparaturzeit oder die Zeit für die korrektive Instandhaltung erfasst.
Schritt 5: Ausrichten und Kalibrieren des reparierten oder erneuerten Bauteils in Abhängigkeit vom System.
Nach der Behebung des Fehlers folgt in der Regel die Ausrichtung und Kalibrierung, die den Beginn der Überprüfung des Zustands des gewarteten Geräts darstellt. Es ist von entscheidender Bedeutung, die entsprechenden Anpassungen vorzunehmen, bevor die Anlage wieder in Betrieb genommen wird. Außerdem muss ein Vergleich der Betriebswerte mit einem festgelegten Standard und eine anschließende Ausrichtung vorgenommen werden, um Abweichungen zu beseitigen.
Schritt 6: Reinigen und schmieren Sie die Ausrüstung sorgfältig.
Nach der Kalibrierung erfolgt wiederum die Reinigung und Schmierung, um das Gerät in einen guten Betriebszustand zu versetzen. Eine gründliche Reinigung des Gerätes und all seiner Komponenten erleichtert nicht nur die Erkennung potenzieller Probleme und verlängert die Lebensdauer, sondern kann auch zu einer höheren Zuverlässigkeit und niedrigeren Betriebskosten beitragen. Es ist außerdem wichtig, ein geeignetes Schmiermittel in der richtigen Menge zu verwenden.
Schritt 7: Prüfen Sie abschließend die Leistung, bevor Sie das System wieder in Betrieb nehmen
Schließlich müssen Tests durchgeführt werden, um zu überprüfen, ob die Leistung der Anlage den vorgegebenen Zustand erreicht. Mit diesem Schritt sind das Logout-Tagout-Verfahren und damit der korrektive Wartungsprozess abgeschlossen. Falls die Messergebnisse zeigen, dass das System zufriedenstellend funktioniert, kann es in Betrieb genommen und der Betrieb wieder aufgenommen werden.
Korrektive (reaktive) Instandhaltung: Noch effizienter mit SafetyCulture (vormals iAuditor)
SafetyCulture (iAuditor): Die moderne Form der Dokumentation von Wartungstätigkeiten. Reagieren Sie blitzschnell auf ungeplante und unvorhergesehene Maschinenausfälle – lösen Sie Probleme im Team mithilfe einer digitalen Betriebsmanagementplattform. SafetyCulture (iAuditor) unterstützt Wartungsteams bei der:
-
Effizienten Durchführung von Instandsetzungsmaßnahmen
Verwenden Sie unsere Vorlagen für Checklisten für Instandsetzungsmaßnahmen auf jeglichem Mobilgerät (Smartphones, Tablets und iPads) – auch, falls Sie gerade offline sein sollten. Erstellen Sie zudem Ihre eigenen Checklisten in minutenschnelle mit unserem Drag-and-Drop-Editor – mit diesem können Sie unsere Vorlagen ebenso leicht und völlig frei an Ihre individuellen Bedürfnisse anpassen. Nach Abschluss der Aufgaben werden automatisch professionell aussehende Berichte erstellt und mit einem Klick an alle betreffenden Mitarbeiter gesendet.
-
Einfachen Meldung von Störungen und Verfolgung von Wartungsmaßnahmen
Melden Sie Maschinenfehler in Echtzeit – inklusive Fotobeweise, welche Sie außerdem zum besseren Verständnis mit Kommentaren versehen können. Weisen Sie innerhalb von unserer Checklisten-App Wartungsmaßnahmen mit Prioritätsstufe und Fälligkeitsdatum an die zuständigen Mitarbeitern zu.
-
Übersichtlichen Darstellung von Inspektionsdaten und Analyse von Wartungstrends
Alle Informationen, die im Rahmen von Instandsetzungsmaßnahmen gesammelt wurden, werden anschließend in übersichtlichen Dashboards dargestellt. Leicht zu bedienende Analysefunktionen ermöglichen es Ihren Betriebsmanagern auf einen Blick Trends zu erkenne, wie z. B. die am häufigsten ausgefallenen Anlagen oder Wartungsprobleme bei bestimmten Geräten und mehr. Starten Sie noch heute Ihre kostenlose SafetyCulture (iAuditor)-Testversion – und bringen Sie Ihre Wartungsprozesse vom Gestern ins Morgen.