Was ist 5S? (Definition)
5S ist eine systematische Methode zur Arbeitsplatzorganisation. Sie basiert auf der Vermeidung von Verschwendung, der Verbesserung des Arbeitsflusses und der Reduzierung von Prozessen. Die 5 S leiten sich von den japanischen Begriffen der fünf Grundsätze des Prinzips ab: Seiri (Sortieren / Selektieren), seiton (Ordnung / Systematisieren), seiketsu (Sauberkeit), seiso (Standisieren / Aufräumen) und shitsuke (Selbstdisziplin / Disziplin). Diese Prinzipien wurden von Toyota ins Leben gerufen und halfen dem Unternehmen maßgeblich dabei die Effizienz seiner Produktion zu steigern.
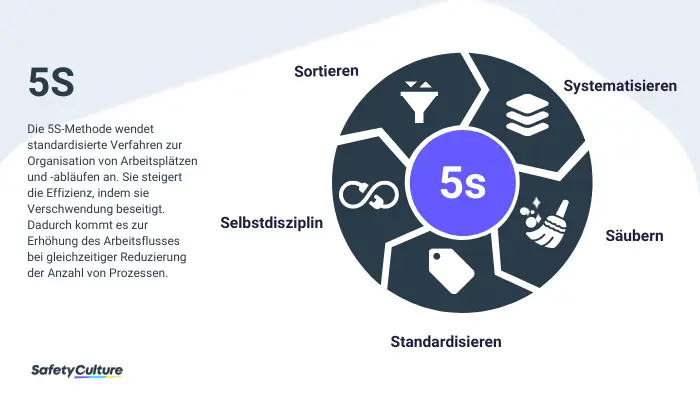
Das Prinzip der 5S-Methode
Geschichte: Wer hat 5S erfunden?
Die Methode wurde im Japan der Nachkriegszeit entworfen (von Hiroyuki Hirano) und in weiterer Folge von Toyota für den Einsatz in der Praxis weiterentwickelt. Die Integration der 5S-Prinzipien in das bereits vorhandene Toyota-Produktionssystem (TPS) war hauptverantwortlich für den Aufstieg des Unternehmens zu einem international konkurrenzfähigen Hersteller hochwertiger Kraftfahrzeuge.
Aufgrund des Erfolges von Toyota begannen auch Unternehmen aus anderen Branchen die Methode in ihre Produktion zu integrieren. HP, Boeing, Harley-Davidson, Nike, Caterpillar und Ford, um nur einige zu nennen.
Warum 5S am Arbeitsplatz oder im Büro?
Die Methode ist eine Startrampe für den Erfolg in der globalen Wirtschaft – falls sie richtig umgesetzt wird. Die Einführung von 5S am Arbeitsplatz führt zu einer effizienteren Arbeitsweise und Verschlankung von Prozessen. Produktionsprozesse laufen beispielsweise effizienter ab, wenn die Mitarbeiter sich bemühen jederzeit die Sauberkeit und Ordnung an ihrem Arbeitsplatz aufrecht zu erhalten. Unternehmen können den Nutzen der 5S-Methode maximieren, wenn sie die Notwendigkeit erkennen, proaktiv Verschwendung von Ressourcen in jeder Form zu reduzieren – sei es durch unnötige Bewegungen, Wartezeiten oder Prozessschritte.
Woran Sie erkennen, dass Ihr Unternehmen reif für die 5S-Methode ist
5S-Lean ist für fast jede Art von Betrieb hilfreich, unabhängig von der Branche. Die Notwendigkeit der Integration der damit verbundenen Praktiken hängt jedoch davon ab, wie dringend Sie Änderungen zum Wohle Ihres Unternehmens vornehmen müssen. Hier sind einige Anzeichen, auf die Sie achten sollten, um zu erkennen, ob Ihr Unternehmen reif für die 5S-Methode ist.
Sie sind unzufrieden mit Ihrer betrieblichen Effizienz
Ganz gleich, ob Sie das Gefühl haben, Ihre Ziele nicht zu erreichen oder nicht mit maximaler Kapazität zu arbeiten: 5S hilft Ihnen dabei, Ineffizienzen zu erkennen – und in weiterer Folge zu beseitigen. Mit Hilfe von standardisierten Arbeitspraktiken, Ergonomie und Arbeitsplatzpflege wird sichergestellt, dass Sie Ihre Ressourcen optimal nutzen.
Die Material-, Herstellungs- und/oder Betriebskosten steigen kontinuierlich
Unternehmen, die noch nicht an kontinuierlichen Verbesserungsprozessen arbeiten, geben oftmals aufgrund von Überproduktion und zu großen Beständen mehr Geld aus als nötig. Die 5S-Methode ist speziell darauf ausgerichtet, Ihre Abläufe zu optimieren und die Verschwendung von Ressourcen zu minimieren.
Mangelnde Konsistenz bei Qualität und Quantität
Betriebliche Unstimmigkeiten bei Qualität und Leistung werden direkt von der Ergonomie des Arbeitsplatzes beeinflusst. Die Einhaltung der 5S-Prinzipien hilft dabei, Ihre Abläufe zu verbessern, indem sie Maschinen, Geräte, Werkzeuge und Materialien so platzieren, dass sie nicht nur leicht zugänglich sind, sondern darüber hinaus auch kein Hindernis für andere Arbeitswege darstellen. Auf diese Art und Weise wird der Zeit- und Energieaufwand für die Suche nach Arbeitsmaterialien und Werkzeugen auf ein Minimum reduziert. Dies führt am Ende des Tages zu einer deutlichen Verbesserung von Qualität und Quantität des Outputs.
Zunahme der Kundenbeschwerden
Steigende Kundenbeschwerden sind ein Warnsignal, das Unternehmen nicht ignorieren dürfen. Da die häufigsten Beschwerden die Produkt- und Servicequalität betreffen, kann der arbeitsplatzzentrierte 5S-Ansatz Ihren Angestellten dabei helfen, sich auf die konsequente Erfüllung der Kundenerwartungen zu konzentrieren.
Vorteile der 5S-Methode
Obwohl viele erfolgreiche Unternehmen, die 5S anwenden, in der Fertigungsindustrie tätig sind, ist die Methode vielseitig genug, um von nahezu jeder Art von Betrieb umgesetzt zu werden – unabhängig von der Größe und Branche. Im Folgenden haben wir Ihnen einige allgemeine Vorteile der Einführung der 5S-Methode aufgeführt:
Abfallvermeidung
Wie der Name schon sagt, zielt 5S darauf ab, das überschüssige “Fett” aus den Geschäftsabläufen zu entfernen, um diese zu verschlanken. Dadurch arbeiten die verbleibenden Prozesse und Komponenten mit maximaler Kapazität.
Konkret geht es bei der Abfallreduzierung um die Vermeidung von 7 Arten von Abfall:
- Überproduktion
Durch die fortlaufende und genaue Erfassung von Verkaufs- und Nachfragedaten können Sie die optimale Anzahl von hergestellten Einheiten pro Produktionslauf ermitteln. So vermeiden Sie die Verschwendung von wertvollem Material durch Überproduktion. - Transport
Diese Art von Abfall bezieht sich auf die unnötigen Schritte, die beim Transport von Materialien von Punkt A nach Punkt B anfallen. - Lagerbestand
Eng mit der Überproduktion verbunden ist die Verschwendung von ungenutzten Materialien und unverkauften Produkten, die Platz wegnehmen und Ihnen damit zusätzliche Kosten für die Lagerhaltung verursachen. - Bewegung
Dies bezieht sich auf ineffiziente Bewegungen, die routinemäßig von Maschinen oder Mitarbeitern ausgeführt werden. Das kann bedeuten, dass Maschinen neu kalibriert werden, um die Abläufe zu optimieren. Oder, dass alte Maschinen durch neue ersetzt werden. Oder dass SOPs aktualisiert werden, um die Effizienz der Mitarbeiter zu steigern. - Warten
Dies ist die Leerlaufzeit zwischen zwei Schritten eines Prozesses, die durch eine fehlgeschlagene Synchronisierung verursacht wird. Im Idealfall sollte ein Betrieb einen Weg finden, unabhängige Prozesse gleichzeitig oder “synchron” ablaufen zu lassen, um die Arbeitseffizienz zu maximieren. - Überoptimierung
Dies bedeutet, dass Produkte mit unnötigen Merkmalen und Ausstattungen versehen werden. Diese bringen dem Kunden zwar keinen wirklichen Nutzen, verschlingen aber natürlich Ressourcen in der Produktion. - Defekte
Dies sind kostspielige Fehler, deren Behebung viel Zeit und Ressourcen in Anspruch nimmt. Durch die Entwicklung und Umsetzung einer SOP auf der Grundlage bewährter Verfahren und die Einbeziehung von Vorsichtsmaßnahmen wie z. B. eines CAPA-Berichts können Sie die Wahrscheinlichkeit von Fehlern einerseits schon einmal verringern. Sowie andererseits im Falle des Auftretens eines Fehlers umgehend mit einer Korrekturmaßnahme reagieren.
Gesteigerte Produktivität
Mit der erfolgreichen Reduzierung von Verschwendung wird in weiterer Folge auch die Produktivität verbessert. Durch die Beschränkung der Anschaffung auf das Notwendige (Geräte, Materialien und Werkzeuge) verbringen die Mitarbeiter weniger Zeit mit dem Sortieren und Einrichten – und mehr Zeit mit ihren wirklichen Aufgaben. Überprüfen Sie bestehende Prozesse und optimieren Sie diese, um mehr Arbeit in weniger Zeit zu erledigen.
Mehr Sicherheit am Arbeitsplatz
Ein weiterer Nebeneffekt der optimalen Arbeitsplatzorganisation ist die Verbesserung der Sicherheit. Ein gut organisierter und aufgeräumter Arbeitsplatz senkt das Risiko von Unfällen durch Ausrutschen oder Stolpern, umstürzende oder herabfallenden Gegenständen und den Kontakt mit Gefahrstoffen.
5S-Workshop und -Zertifizierung
So einfach die 5S-Prinzipien auch erscheinen mögen, der beste und effektivste Weg Ihr Team auf die Implementierung der Methode vorzubereiten, ist eine Schulung mit abschließender Zertifizierung. Auch wenn der genaue Lehrplan in verschiedenen Schulungsprogrammen variieren kann, ist es jedoch wichtig, eine solche abzuhalten. Sie hilft Ihrem Team dabei, jeden der fünf 5S-Pfeiler in seinen Grundsätzen zu verstehen. Dies erleichtert in weiterer Folge die Umsetzung am Arbeitsplatz in erheblichem Ausmaß.
Wie sieht ein 5S-Schulungsprogramm aus?
Die Schulungsteilnehmer müssen in der Regel sowohl Einzel- als auch Teamaktivitäten zu jedem der 5 Grundsätze durchführen. Die Schulung wird im Idealfall direkt am jeweiligen Arbeitsplatz durchgeführt, um den Lerneffekt für die Teilnehmer zu maximieren.
Wo kann ich eine 5S-Schulung und -Zertifizierung erhalten?
Eine Reihe von Organisationen bieten solche an. Schulungspakete können ebenso Webinare und Vorlagen für Checklisten enthalten. Diese können Sie anschließend verwenden, um die richtige Anwendung der 5S-Grundsätze durch die Teilnehmer an ihrem jeweiligen Arbeitsplatz zu bewerten.
Erstellen Sie Ihren eigenen 5S-Aktionsplan
Nicht genau zu wissen, womit man beginnen soll, kann entmutigend sein. Besonders, falls man ein bisher unbekanntes Konzept zur Anwendung bringen möchte. Im Folgenden finden Sie deshalb einige grundlegende Schritte zur effizienten Etablierung der 5S-Methode in Ihrem Unternehmen.
- Sichten Sie die im Betrieb vorhandenen Probleme
Damit Sie Ihre Ausgangslage leichter einschätzen können, erstellen Sie eine Liste der aktuellen Probleme, die Ihr Unternehmen plagen – und ordnen Sie diese nach ihrer Dringlichkeit. Auf diese Weise können die wichtigsten Aspekte identifiziert werden, die vorrangig behoben werden müssen. - Verschaffen Sie sich einen Überblick über die verfügbaren Ressourcen
Um den potenziellen Nutzen für Ihr Unternehmen zu maximieren, müssen Sie sich zuerst einmal über Ihre verfügbaren Ressourcen im Klaren sein. Nur, falls Sie genau wissen, was Ihnen aktuell zur Verfügung steht, können Sie bestimmen, wie viel Zeit, Material und Personal Sie für die Umsetzung der 5S-Methode aufwenden können. - Erstellen Sie eine 5S-Checkliste
Nachdem Sie in Schritt 1 die Probleme identifiziert und in Schritt 2 die verfügbaren Ressourcen erhoben haben, erstellen Sie eine Checkliste. Dies dient dazu, um sicherzustellen, dass alles, was getan werden kann, auch getan wird. Diese muss nicht übermäßig kompliziert und mit unnötigen Details gespickt sein. Eine effektive Checkliste muss im Endeffekt nur zwei Dinge enthalten: Was zu tun ist und ein Ja- oder Nein-Feld, um die Erledigung anzuzeigen. Eine Checkliste hilft den Arbeitnehmern nicht nur, sich besser zu organisieren, sondern motiviert diese auch, produktiver zu sein. Vorgesetzte und Manager profitieren gleichermaßen von der Verwendung von Checklisten, denn die einfache Aufschlüsselung der Aufgaben stärkt ihr Vertrauen in die Delegation von diesen. - Starten Sie Ihr 5S-Lean-System
Die vorangegangenen Schritte dienen dazu, das angepeilte Ziel festzulegen – die Maximierung Ihres Geschäftspotenzials. Im letzten Schritt geht es nun darum, Ihre Pläne in die Tat umzusetzen. Achten Sie bei der erstmaligen Durchführung Ihres 5S-Programms genau auf Komplikationen und andere Faktoren, die Sie in der Planungsphase nicht vorhersehen konnten. So verbessern Sie sich und Ihr System fortlaufend.
5S-Beispiel
Die Kenntnis der oben beschriebenen Grundprinzipien von 5S stellt bereits die Grundlage für Ihren Erfolg dar. Ein Musterplan, der Ihnen als Leitfaden dient, wird noch weiter dazu beitragen, dass Ihre erste 5S-Implementierung reibungslos verläuft.
S1: Sortieren / Selektieren |
Aktionsplan:
Entfernen Sie Maschinen, Geräte, Werkzeuge und Materialien, die nicht mindestens einmal pro Woche benutzt werden, von allen Arbeitstischen, Produktionsflächen und Arbeitsbereichen. Diese Gegenstände sollten mit einem Etikett versehen und in einen dafür vorgesehenen Bereich gebracht werden, wo sie 7 Tage lang verbleiben. In dieser Zeit kann das Personal die Gegenstände durchsehen und diejenigen zurückholen, die für die Durchführung ihrer Arbeit doch noch benötigt werden. Alle nach Ablauf des Zeitraums nicht abgeholten Gegenstände werden entsorgt. |
Informationen zum Etikett:
Das an jedem Gerät oder Gegenstand angebrachte Etikett muss die folgenden Informationen enthalten:
|
Nicht vergessen:
|
S2: Systematisieren / Ordnung |
Aktionsplan: Beginnen Sie damit, den idealen, ergonomischen Standort für alle Maschinen, Geräte, Materialien und Werkzeuge zu ermitteln. Faktoren, die es dabei zu berücksichtigen gilt, sind beispielsweise der Abstand zwischen zwei Maschinen, die nacheinander eingesetzt werden. Oder der Abstand zwischen dem Materiallager und dem Produktionsbereich. Das Ziel von diesem Vorgang ist, alle Einrichtungen an ihrem jeweils sinnvollsten Standort zu platzieren, um die Arbeitseffizienz zu maximieren. Führen Sie anschließend ein Brainstorming mit den wichtigsten Interessengruppen durch, um herauszufinden, ob die vorgeschlagenen Änderungen durchführbar sind. Besprechen Sie Logistik, Zeit- und Budgetvorgaben, Raumaufteilung usw. Nehmen Sie außerdem Fotos von jedem Bereich auf, bevor Sie die genehmigten Pläne umsetzen. Und verfolgen Sie im Anschluss die erzielten Verbesserungen (oder auch Verschlechterungen), um die Auswirkungen der vorgenommenen Änderungen zu messen. |
Zu beachtende Punkte:
|
Nicht vergessen: Verwenden Sie eine Checkliste, um die Auswirkungen der vorgenommenen Änderungen nach einem vereinbarten Zeitrahmen zu bewerten. |
S3: Sauberkeit |
Aktionsplan: Beginnen Sie mit der Beseitigung von Staub, Schmutz und Ablagerungen an allen Arbeitsplätzen und weiteren Bereichen. Beauftragen Sie dafür am besten ein renommiertes externes Reinigungsunternehmen, um sicherzustellen, dass ordnungsgemäße Verfahren angewandt werden und Geräte sowie Einrichtungen vor Schäden geschützt sind. Beauftragen Sie zusätzlich einen Angestellten Ihres Unternehmens mit der Überwachung der Reinigung. Damit garantieren Sie, dass alle Geräte, Werkzeuge, Materialien, Einrichtungen und Lagerbereiche am Ende angemessen gereinigt und aufgeräumt sind. Ermitteln Sie als Nächstes die Quellen von Staub, Schmutz und Ablagerungen und arbeiten Sie daran, diese zu minimieren. Oder im besten Fall komplett zu beseitigen, falls möglich. Wenn sich zum Beispiel zu schnell Staub im Büro ansammelt, sollten Sie die Filter der Klimaanlage überprüfen lassen, da diese möglicherweise gereinigt oder ausgetauscht werden müssen. Erstellen Sie schließlich Protokolle wie eine Checkliste für einen regelmäßigen Reinigungsplan, um in Zukunft die Ordnung und Sauberkeit am Arbeitsplatz zu gewährleisten. |
Zu beachtende Punkte: Neben der Sauberkeit am Arbeitsplatz wird von den Arbeitnehmern auch Folgendes erwartet:
|
Nicht vergessen:
|
S4: Standardisieren |
Die ersten drei Schritte des Sortierens, Ordnens und Saubermachens zielen darauf ab, einen Arbeitsplatz durch Ergonomie und Organisation zu revitalisieren. Der vierte Schritt besteht nun darin, erfolgreiche Konzepte zu übernehmen und sie im gesamten Unternehmen als Standard zu etablieren. Aktionsplan: Beginnen Sie mit einer Besprechung mit den wichtigsten Interessengruppen und bestimmen Sie Mitarbeiter, die für die Standardisierung in den verschiedenen Abteilungen und Schichten zuständig sind. Idealerweise sollten es Abteilungsleiter oder zumindest höhergestellte Angestellte sein. Sobald diese feststehen, erstellen Sie ein Protokoll darüber, wie die Standardisierung der neuen Prozesse umgesetzt werden soll. Im Folgenden sind die zu behandelnden Punkte aufgeführt:
|
Zu beachtende Punkte: Stimmen Sie sich mit dem ISO-Koordinator oder Compliance-Beauftragten ab, um sicherzustellen, dass alle Aktualisierungen und Änderungen mit den derzeit gültigen Normen in Übereinstimmung sind. |
Nicht vergessen: Senden Sie nach der Umsetzung ein Rundschreiben an alle Interessengruppen, um sicherzustellen, dass jeder betroffene Mitarbeiter sich auf dem aktuellen Stand befindet. |
S5: Selbstdisziplin (zur Aufrechterhaltung) |
In diesem Schritt geht es darum, die von S1 bis S4 erzeugten positiven Effekte aufrechtzuerhalten. S5 ist also vor allem ein 5S-Audit, um sicherzustellen, dass die neu eingeführten Standards konsequent befolgt werden. Aktionsplan: Sobald die neuen Standards eingeführt worden sind und alle Beteiligten deren Umsetzung bestätigt haben, rufen Sie eine weitere Sitzung ein. Diese dient zum Erstellen eines Audit-Plans, mit dem in Zukunft sowohl die positiven als auch die negativen Auswirkungen der durchgeführten Änderungen verfolgt werden. Nachfolgend finden Sie die wesentlichen Elemente eines wirksamen Prüfplanes:
|
Zu beachtende Punkte:
|
Die Branchen, die am meisten von der 5S-Methode profitieren
Nachdem sie zunächst durch die Optimierung von Fertigungsprozessen in der Produktion an Popularität gewonnen hatte, entdeckten auch Unternehmen außerhalb der Fertigungsindustrie die Vorteile der 5S-Methode. Diese ist nämlich vielseitig genug, um auch für andere Arten von Geschäftsabläufen eingesetzt zu werden. Im Folgenden sind einige der wichtigsten Branchen aufgeführt, die von ihrer Implementierung profitieren können.
Die 5S-Methode in der Produktion: Schlanke Prozesse steigern die Konkurrenzkraft
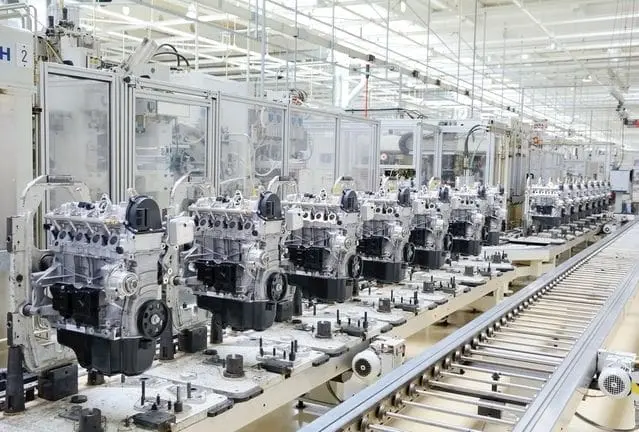
Die 5S-Methode in der Fertigung: Mehr Effizienz und Produktivität in umkämpften Märkten.
In den 70er Jahren von Sakichi Toyoda entwickelt und in das TPS (Toyota Production System) integriert, trug 5S dazu bei, Toyota zu einem der führenden Automobilhersteller der Welt zu machen. Sowohl in den Montagewerken als auch in den Büros sind die Arbeitsmaterialien leicht zugänglich. Außerdem wird die Arbeitsfläche durch die Festlegung von Bereichen für Möbel, Geräte und Einrichtungsgegenstände maximiert. Toyota verwendet außerdem zahlreiche Checklisten, um sicherzustellen, dass alle 5S-Aktivitäten konsequent durchgeführt werden. Aufgrund des Erfolgs von Toyota wurde 5S zu einem Standard für Fertigungsunternehmen, die ihr Potenzial maximieren wollen.
Medizin und Gesundheitswesen: 5S als Retter in der Not
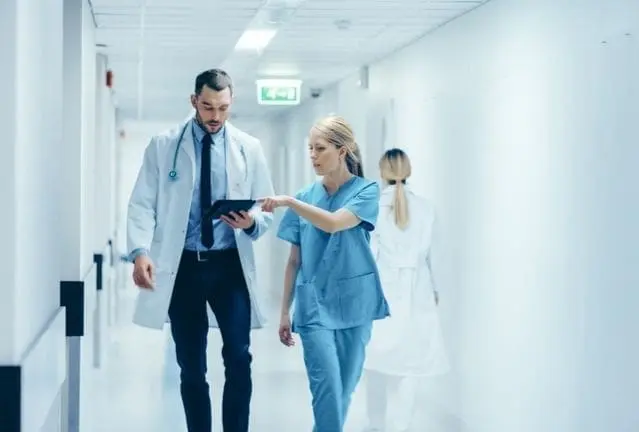
Die 5S-Methode im Gesundheitswesen als Retter in der Not.
In Krankenhäusern und Arztpraxen kann 5S-Lean eingesetzt werden, um die ordnungsgemäße Kennzeichnung von Medikamenten und Utensilien zu gewährleisten oder die Patientensicherheit zu verbessern. Der Ansatz erhöht genauso die allgemeine betriebliche Effizienz medizinischer Einrichtungen, da er es den Mitarbeitern erleichtert, ihre Arbeit in einer optimierten und übersichtlichen Umgebung auszuführen.
Einzelhandel: Ordnung und Sauberkeit Dank der 5S-Methode
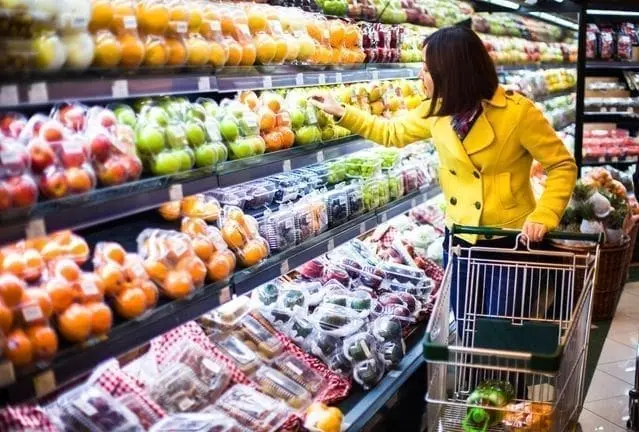
Das 5S-Prinzip angewandt im Einzelhandel. Ordnung und Sauberkeit anstatt Chaos im Regal.
5S Lean ist die perfekte Lösung für die Einzelhandelsbranche, da es sowohl die Sortierung als auch die Organisation fördert. Zwei Elemente, die den Beschäftigten gleichermaßen wie den potenziellen Kunden zugute kommen.
- Seiri wird für die Sortierung der Bestände im Lager eingesetzt, damit die Mitarbeiter bestimmte Artikel leicht finden können. Es kann außerdem für die Regalbestückung verwendet werden, um sicherzustellen, dass die Kunden das Gesuchte problemlos finden können.
- Seiton wird angewandt, indem Lagerbestände und Geräte zur einfachen Identifizierung beschriftet und an den immer selben Orten aufbewahrt werden – übersichtlich und leicht zugänglich.
- Seiso wird eingesetzt, um das Lager und die Bestände sauber und gepflegt zu halten.
- Seiketsu und Shitsuke hingegen beziehen sich auf die Einführung von allgemeingültigen Standards und Protokollen, um sicherzustellen, dass die Qualität in allen Niederlassungen nicht nur jederzeit gewährleistet, sondern auch jederzeit dieselbe, ist.
Hotellerie und Gastgewerbe: Höhere Kundenzufriedenheit durch 5S
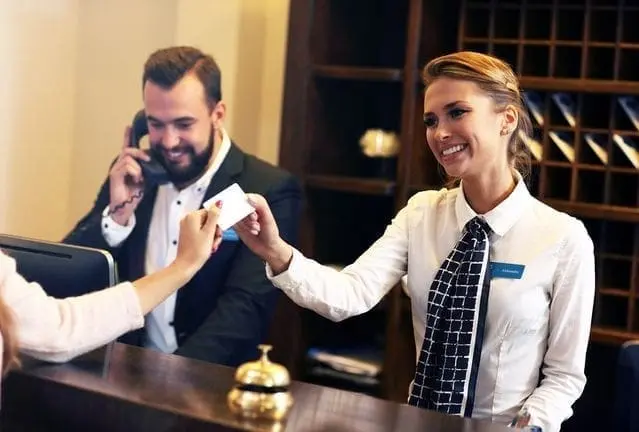
Das 5S-System eignet sich ebenso bestens für Hotellerie und Gastgewerbe.
Die Ziele von Hotels, Restaurants, Ferienanlagen und anderen Unternehmen des Gastgewerbes stimmen natürlich perfekt mit den 5S-Prinzipien überein. Organisation, Ordnung, Sauberkeit und Konsistenz – Qualitäten, die Kunden in einem Gastgewerbebetrieb suchen – werden durch die 5S-Methode erreicht. Die Integration von dieser in die Kultur des Gastgewerbes verbessert die betriebliche Effizienz, maximiert die Ressourcen und erhöht die allgemeine Kundenzufriedenheit.
Computer und Technologie: Systematik mit dem 5S-System
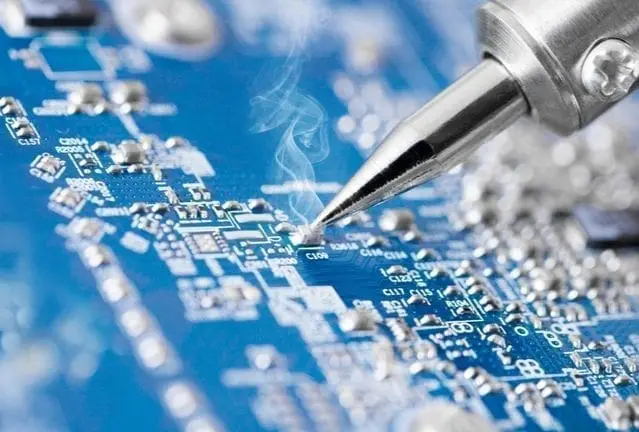
Das Prinzip der 5S-Methode ist hervorragend für die logischen Abläufe in der IT und Computerindustrie geeignet.
Die Computer Systems Division von Hewlett-Packard nutzt 5S, um den Systembau effizienter zu gestalten. Wenn Computerteile sortiert, ordnungsgemäß beschriftet und in leicht zugänglichen Bereichen gelagert werden, wird die Fertigung schneller und einfacher. Darüber hinaus kann 5S auch zur Rationalisierung der Softwareentwicklung eingesetzt werden. Die Kennzeichnung häufig genutzter Werkzeuge, um sie leicht auffindbar zu machen, spart Zeit und fördert die Produktivität. Die Standardisierung von Arbeitsverfahren hält die Leistung der Mitarbeiter in verschiedenen Büros und Schichten konsistent.
5S-Prinzip im Bildungswesen
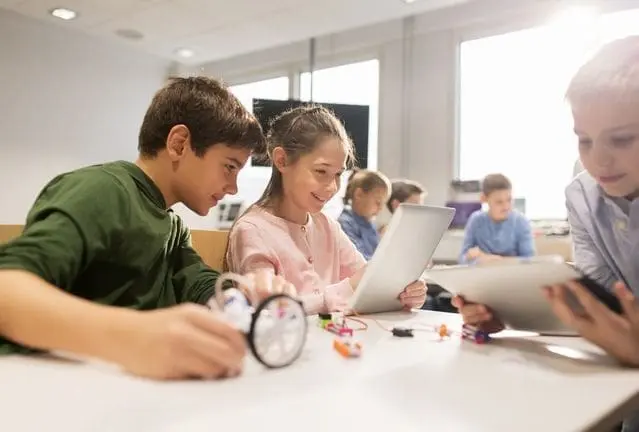
Die 5S-Methode hat ebenso klare Vorteile für das Bildungswesen. Bringen wir unseren zukünftigen Generationen schon früh die richtigen Werte bei.
Schulen müssen ein angenehmes, lernförderndes Umfeld schaffen, um effektiv zu sein. Klassenzimmer profitieren von 5S-Lean, indem alles Unnötige aus dem Klassenzimmer entfernt wird. Einschließlich überflüssiger Stühle, Tische, Schränke und Materialien, um die Konzentration der Schüler zu fördern. Danach können die verbleibenden Möbel und Einrichtungsgegenstände in Ordnung gebracht werden, um den vorhandenen Platz zu maximieren. Letztendlich bietet 5S einen Rahmen für die Schaffung eines optimalen Lernumfelds in jedem Klassenzimmer.
5S-Methode im Büro
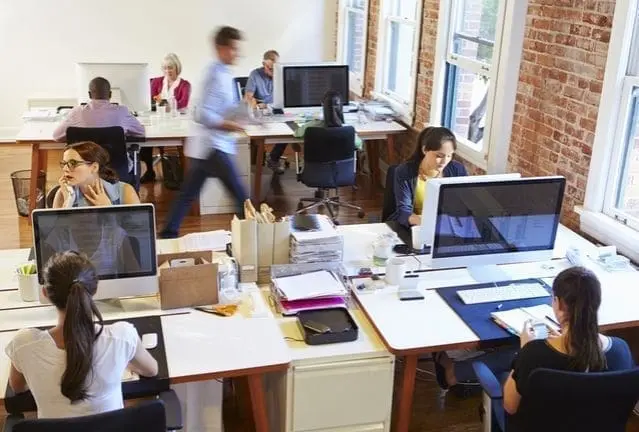
Die 5S-Methode bringt in Ordnung in jeden noch so betriebsamen Büro-Arbeitsplatz.
Unabhängig von der Branche verfügen fast alle Unternehmen über eine Betriebszentrale, die sich hinter den Kulissen um die Geschäftsabläufe kümmert. In Büros, die nicht nach der 5S-Lean-Methode (oder einer ähnlichen) arbeiten, herrschen oft unordentliche Verhältnisse und unaufgeräumte Arbeitsbereiche. Ein solches Arbeitsumfeld schadet der Produktivität und fördert ungewollt die Verschwendung von Ressourcen. Die Beseitigung unnötiger Gegenstände in Verbindung mit der Anwendung der 5S-Regeln am Arbeitsplatz steigert die Effizienz und senkt die Betriebskosten.
Wollen Sie noch einen Schritt weitergehen? Dann kombinieren Sie die 5S-Methode mit zusätzlichen Sicherheitsaspekten, und Sie gelangen zur 6S-Lean-Methode.